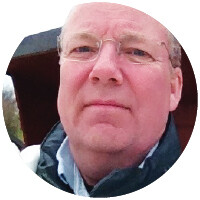
Let’s begin, Peter, by telling our readers briefly about your background in shipping leading up to today.
I began my career in logistics as a messenger boy at age 14, finished my traineeship in 1978, moved to the UK, and stayed for two years working as a TIR clerk, and then moved back to Denmark, working for the first time in a project department. I then joined the Danish School Of International Marketing and Export, moved into sales, and held jobs as a sales manager in various companies until luck struck.
In 2006, I became employed as logistics manager in Suzlon, an Indian wind turbine manufacturer that had just set up a global HQ in Denmark. My knowledge specifically of wind turbines was essentially null, but I knew a lot about logistics.
In the beginning, the support was basic. The transport and handling manuals were very basic. This was the beginning in a department where many things were still under development, and basici.e., transport & handling manuals were almost non-existant in the company so “challenges” had to be solved on the fly & the learning curve was brutal.
During the turbine recession in 2008-2009, I was headhunted by a Danish WTG manufacturer. From there I went to the Danish project forwarder Martin-Bencher, where I assisted in setting up a department for transport of wind energy equipment and also doing consultancy for companies like Alstom on the Haliade 150 5mw platform & Leighton’s in Australia on a Mongolian project.
I have always been curious about what I was transporting. Understanding a client’s product, in my opinion, gives you a better angle to understand the clients and their client’s needs.
Since I was young, I have enjoyed sailing in our family sailboat. When I got older I took flying lessons and am today a private pilot in my spare time. My hobbies seem to revolve around the same principle that makes a wind turbine blade rotate and generate power, so you can say that my hobby now encompasses my job or vice versa.
You have a particular experience and knowhow in the transportation of wind turbines, both deep sea and inland. Can you, in detail, tell our readers about some of the projects you have handled worldwide, if you can elaborate also a bit on some of the major headaches that you have faced?
Most of my jobs have been in Matrix organizations, where cooperation is of the essence—no cooperation = no results on your own part. In Suzlon, India was responsible for sending the turbines to the designated ports in Denmark and later US and Australia then was responsible for the port and quay designation, transport to site, storage etc.
My first job was to negotiate a charter with BBC for 10 vessels. The shipment was scheduled over 12 months, but unfortunately, the contracts for the turbines were delayed, and subsequently, we had to postpone the departures. BBC was good about it; they could have demanded payment for non fulfilment, but refrained, and with 12 months delay, we started shipping the towers to the US.
On the vessel side, operations require that you get the best help possible to learn from, and I was lucky to have Captain Inder Malhotre and Peter Holt. Both were exceptional in drawing in the detail, lashing, on board crane operation, and all the intricacies that can hit you like a hammer if you are not aware.
In Nicaragua, we were to erect 19 turbines, and the towers were to be supplied to Nicaragua from Spain and Germany. With the heaviest tower section weighing approximately 70 tons, suitable moving equipment for the port operation was not readily available. Furthermore, the slings for the shore operation were not available. They had not arrived in time for the discharge, so we had to improvise. The port bolted 2 mafis (mobile loading platforms)together with 32 mm bolts, but after moving the first section, the bolts broke with a loud crack, and we were faced with a major problem: how do you find a lowloader trailer with a payload of 70 tons in Nicaragua? In the end, we started transporting the sections with 2 caterpillar trucks running side by side, the finest ballet I have ever seen.
On Jeju island Korea, a vessel came in from India with 9 turbines onboard. However, the special bolts used for lifting the 20-ton hubs were not given to the ship at the time of loading in India, so now we were standing with an item that most looks like a giant steel football. You can’t lift it in slings because of its shape, so without bolts, there would be no lifting.
The captain served me notice that if we did not begin lifting within 3 hours, he would proceed to Japan, and then we could pick up our hubs there. It was the weekend, and no equipment was available on the island. An hour before the deadline, the chief mate took one of the turnbuckles apart, and we tried it in the thread of the hub. With one complete diameter embedded in the thread, the engineer that was on the phone from Denmark gave the go ahead to lift, and we finished the job.
Luck sometimes plays a part in the operations.
Somehow, it is the challenges that remain with you; the smooth sailing does not make such an impression.
Every Tom, Dick and Harry in the project freight forwarding field nowadays calls themselves “renewable energy experts”. What is your comment to that? Is moving renewable energy components really that much different from, say, plant machinery or other heavy items?
Whenever you undertake the transport of something that is large or heavy or both, you need to think through what challenges lie ahead, be it road structure, port layout and accessibility, legal requirements and permits, crane availability in ports and on site, etc. As the cost of standstill is very high, you need to plan so that the equipment is operating as close to capacity as possible, taking downtime for maintenance into the equation. This is no different whether you are moving a generator, a cracking tower or a wind turbine. In wind turbines, you don’t do a lot of skidding, which you may do on generators as they may have to be placed into buildings. On the other hand, blades on WTG’s are long, and you need to have special trailers that fit the requirement of the blades which may not be readily available locally.
Describe for us, please, the components of a typical wind turbine and elaborate if you will on the development in size since you started until now. Offhand, would you recommend any specific shipowners as having exceptionally good knowhow in this field?
An onshore turbine normally consists of the following main components: 3 Blades, 1 Hub, 1 Nacelle & 1 tower split in sections & nosecones. To keep the weight of the nacelle down, it is sometimes split into individual components, i.e., gearbox and generator.
When I started with WTG transport, a turbine had an output of about 2 mw. A blade (not a wing) was about 40-50 meters long, and weighted about 7 tons. The nacelle (the generator sitting on top of the tower) weighed about 75 tons and the hub about 20 tons. The total tower was 80 meters high and weighed in at about 185 tons in 4 sections. Today, a large land turbine blade is 80+ meters long (roughly twice as long as before) and weighs about 35 tons (about 5 times heavier). The nacelle today is about 400 tons (more than 5 times heavier), the tower is 100 meters high (an increase of 20 M), and the turbine is producing 6 mw (roughly 3 times as much output).
For offshore turbines, Siemens has just announced a 14mw with 108 meter long blades. The rotor diameter will be 220 meters.This means that one blade is wider than the total wingspan of an airbus A380 (79.8 meters).
Everything gets bigger. This is a challenge in all aspects of the transport chain. The trucking companies need new equipment capable of supporting the longer and heavier blades. The nacelles need to be transported on equipment with more axles to keep the axle weight down in order not to destroy the roads. The lifting capacity and reach of the cranes need to increase as the tower height is increasing (in order to hold the longer blades). The shipping tonnage able to move, lift, and install the turbines for offshore installment needs to fulfill the same requirements. I know of no other industry in which the sizes, weights, and outputs have increased so much within such a short time span.
What is the main component for the successful completion of a wind turbine project?
Planning, planning, planning…and some luck.
For a project to be a success the necessary permits must be in place. Contracts with suppliers should be closed. Agreements with share and stakeholders in place. Ports, trucking companies, cranes, etc. must be arranged and schedules agreed on.
A holistic view of the process from all parties eases the process. Often, you have to move a number of items from several different suppliers in different countries to a location—often an elevated one—where there is no electricity, roads or facilities. In addition, you are working with and around a multitude of sub-suppliers that all have their own agenda and various cultures. As a result, cooperation is of the essence.
You have a job to do, and so does everyone else. Look at it like an ant hill; everybody is moving around to do something, and sometimes you get in the way of somebody. , eEven worse, two of your own simultaneous operations are in the way of each other or having to use the same crane at the same time. Who do you favor?!
After contracts, time schedules agreed to by all parties are very important and, especially, the wish for all that the total project is a success.
Rest assured, something will eventually mean that your schedule is changed, and then remember a smile goes a long way to break down tension in all languages.
I recall that you had also done major road surveys including a trip into the Mongolian Gobi Desert. Tell us more? How was that?
A former colleague of mine, a Mr. Bo Drewsen (the editor of this publication), found out that an Australian company was going to erect some four turbines outside Ulan Bator, the capital of Mongolia. He also secured us the right to bid for the project and asked me, as someone responsible for WTG projects, to undertake the bidding. With Mongolia being new territory, he suggested that I fly to Beijing and then drive up through the Gobi desert to get a feel for the land. This was a 3-4 day drive, and at the time, I thought it was a waste of time (but did it anyway).
Never have I been so wrong!
After three days in a “tumble dryer” (Toyota Land Cruiser) with two of my colleagues, one of which was David Xu now with the Sino Project, we arrived in Ulan Bator and put together the proposal. Most importantly of all, I was able to discuss in detail the challenges of pulling the equipment over850 km (roughly) of which at least 200 km was washboard sand—a landscape that made everything that was not very very securely fastened break loose.
We did not, unfortunately, get the project, but later, I was contacted by an old colleague asking if we could assist the owner of the project as they were having difficulties with their tower transports. The attachments of the cables in the towers could not withstand the constant g-loads during the drive over the washboard.
When our readers would like to get hold of you to know more about the business and about you, how is it best for them to do that?
All contacts are welcome by mail at peter@schou.be or by phone +45 2949 9715